Driven by legislation and market requirements, the boiler industry is moving toward burners that produce low nitrogen oxide (NOx) emissions without external flue gas recirculation (FGR). The burners must also be suitable for new, renewable fuels.
This article will examine developing power plant-scale burners, compact and simpler burners without external FGR, and the evolution of already proven ultra-low NOx burners.
Eliminating Nitrogen Oxides
NOx is a gas formed by nitrogen and oxygen. In the atmosphere, NOx reacts with hydrocarbons (HCs) to form small particles. NOx emissions cause breathing difficulties in humans and animals, increase the risk of cardiovascular disease, and produce many other adverse effects. NOx also acidifies and eutrophicates soils and water bodies and damages plants.
In China, strict legislation came into force in early 2017, requiring NOx emissions to be below 15 ppm (ref. O2 3%). This has been one of the major factors behind Oilon’s efforts to further decrease the emission levels of its power plant-scale burners in the 650- to 9,500-BHP range.
“We learned about the new legislation nine months before it came into force,” said Joonas Kattelus, chief technology officer of Oilon Technology Oy (Ltd). “We got off to a fast start, and in February and March 2017, we had the first 3,500-BHP pilot on the field in China. The rest is good history.”
According to Kattelus, these burners are a very important product group for Oilon, and their success in the market has been good. However, low-NOx performance does not have the same importance in all markets. China’s requirements are the most stringent of individual countries. Russia, on the other hand, has not traditionally been very interested in NOx emissions, but at the moment, interest is also growing in major Russian cities. In the U.S., NOx restrictions have long been applied with state-specific weightings, and their importance is still growing.
Ridding the Market of FGR
“Market requirements have changed, and competitors have entered the market with very similar technologies,” Kattelus said. “Our burner technology is based on internal and external flue gas recirculation and fuel and air phasing. However, demands are tightening, and the market wants to get rid of external flue gas recirculation.


“External recirculation piping takes up space, increases costs, and shortens system life due to condensation,” he continued. “In the development of the new burner family, we have succeeded in improving the internal recirculation of flue gases so that, in many cases, external recirculation can be completely eliminated.”
Product development has done a lot of work to solve the problems related to internal recirculation. In external recirculation, a fan can be utilized, but, in the internal, a natural circulation must be created by the design of the combustion head. In external recirculation, the flue gases cool, and the durability of the materials is not a similar problem as in the internal recirculation of hot gases. Due to the flue gas temperature, internal recirculation also does not reduce NOx as effectively as external recirculation.
NOx emissions and other performance parameters always vary depending on the furnace geometry and conditions. The simulation software allows one to calculate the exact case-specific operating points and select just the right burner for each application.
The Two Product Families Continue to Develop
In the new burner family, the flue gases are sucked into the combustion head with the ejector principle with both the air pressure of the combustion head and the gas pressure of the main gas. If necessary, the principle can also be used in external FGR applications as well as in hot air applications. Externally, the new burner family looks exactly like the previous one, but the combustion head is completely different.
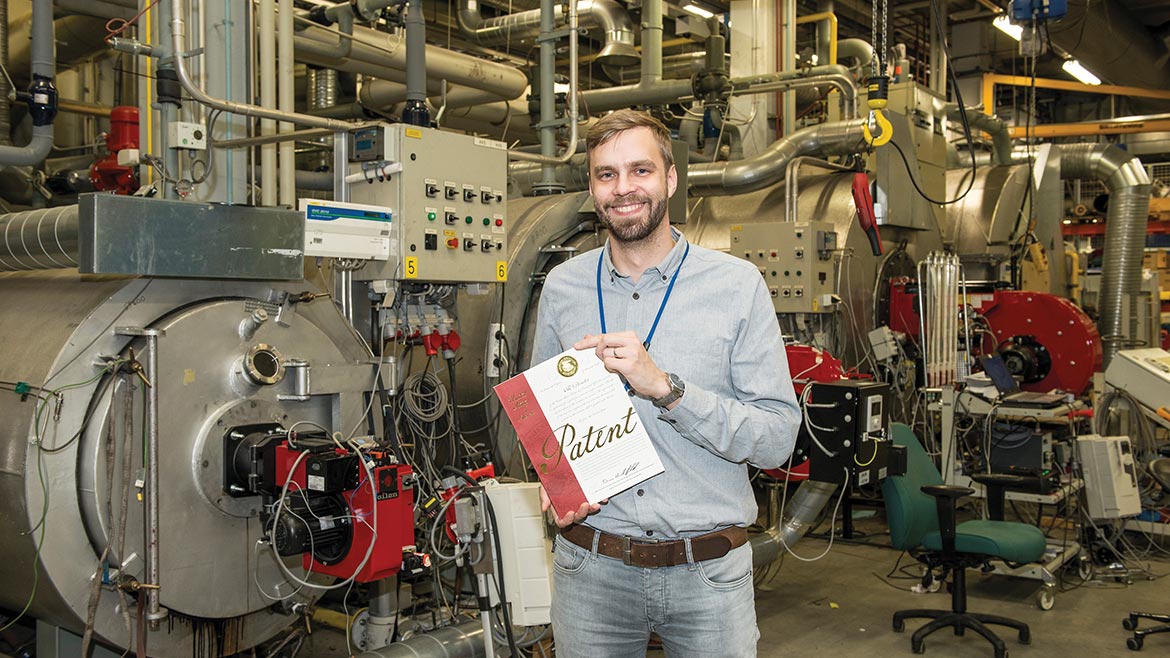
According to Kattelus, the product development of the new burner family is at a good stage. In the laboratory, they have reached 15-ppm emission levels, and the targets have been met in the first European pilot installation. There are two pilots in operation in China — one with a capacity of 7,000 BHP. Field tests are ongoing and progressing steadily toward the goal. Pilot sites are being looked for in North America.
“The new burner family is not a product that is supposed to displace the previous one – both are needed,” Kattelus said. “The megatrend in the market is a changing fuel mix. Biogas, bio-oil, process by-products, and hydrogen combustion are making their entry. Inquiries about them are growing, and we want to respond to the need. Biofuels burn slightly differently than fossil fuels; for example, the calorific value and available pressure may be lower. Hydrogen, on the other hand, reacts strongly and overheating and emissions must be controlled. Hydrogen produces NOx like any other fuel — even more.
“We invest heavily in product development and low-NOx technology,” Kattelus continued. “The original burner family will be developed to be more versatile for new fuels, and the new one will be more low-emission.”

The Patented LN30 Burner Family
In the spring of 2020, Oilon introduced a completely new burner family with four models in the power classes 90-490 BHP. These burners are designed for industrial use and for the production of hot water and steam. Already at the demonstration stage, they achieved ultra-low NOx levels in natural gas combustion, less than 9 ppm, and, at best, less than 5 ppm. The premix burner has a long, tubular combustion head.
The LN30 product family was featured in the fall 2020 issue of Today’s Boiler magazine.
“In California, legislation will be in place from the beginning of 2023 that will require less than 5-ppm emission levels for most natural gas combustion applications,” says Kattelus. “This is the level we set out to achieve for the LN30 burners, and, in the laboratory, we have achieved it.
“In the fall of 2021, we launched our first field reference with Nationwide Boiler Inc.,” continued Kattelus. “In it, we have used a burner model that produces 270 BHP of power in that application. Infield tests, we have successfully achieved below 5 ppm emission levels throughout the power range.
“One strong piece of evidence of the level of our technology is that the U.S. patent and trademark office granted a patent for LN30 burner technology in the country on July 13, 2021. And, California is a great place to unveil technology that others don’t have. Even the FGR does not reliably deliver as low emissions.”
Until now, combustion plants have had to use flue gas after-treatment, because, otherwise, it has not been possible to achieve sufficiently low emissions.
“With this product family, we profile ourselves to compete against catalytic flue gas cleaning,” concluded Kattelus. “It does not require FGR, catalyst, urea, flue gas cleaning, or combustion air filtration. Both fixed and operating costs are cheaper.”